Transforming dentistry to improve oral health globally
Article
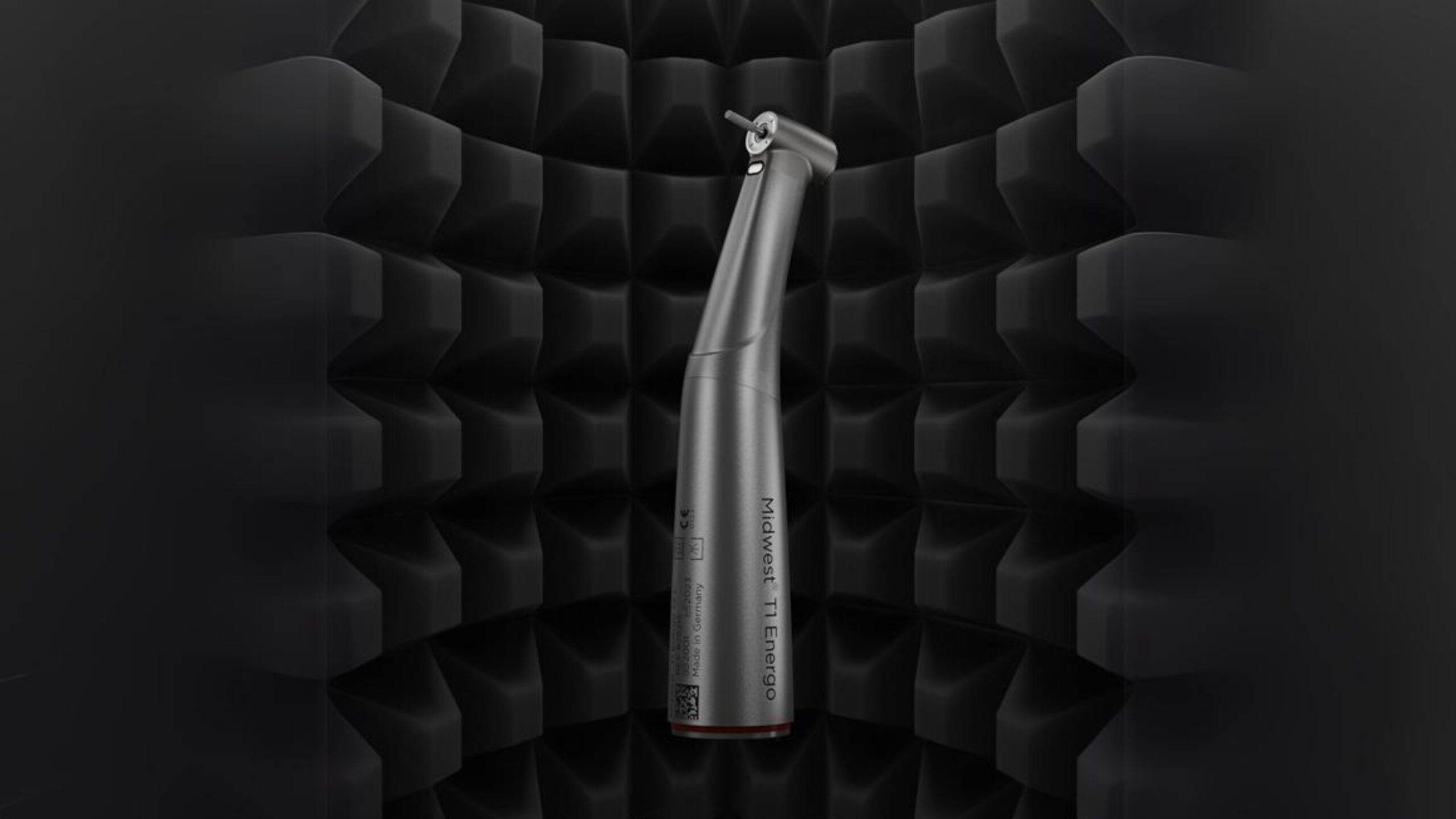
Bensheim, 14. March 2024.
Innovating for Healthier Smiles
Visiting your dentist is seldom fun, but for some people it is just fear – one important reason for this is the operating sound of dental handpieces. Just the thought of this leads to goose bumps. Dentsply Sirona as one of the leading companies in the dental market always tries to optimize its products – to empower millions of customers by innovative solutions to preserve and create healthy smiles.
One important task is to continuously optimize the quality of dental contra angle instruments while ensuring low costs in manufacturing. In this context Dentsply Sirona is part of the DAT4.ZERO Project, which has received funding from the European Union´s Horizon 2020 program. The goal of this project is to elevate the quality assurance process to new heights. Following the vision of digital, fast quality control loops different ideas are followed up in the project – always with the focus to realize a ZERO DEFECT Manufacturing.
A promising concept focuses on using process data to control complex production processes. The goal is to reduce scrap by fast, data driven decision making – without using additional and time-consuming downstream processes. Together with different partners in the project, mainly here the KIT, Dentsply Sirona evaluated different technical solutions and tested the integration of a structure borne sound sensor in a serial production machine in Bensheim, where the biggest site of Dentsply Sirona is located. It was selected for its high Technology Readiness Level (TRL) and promising initial tests. This approach is not just about enhancing a single product feature; it’s a strategic move to ensure the competitiveness of Dentsply Sirona in the dental equipment market.
The technical solution developed within the DAT4.ZERO project involves a sophisticated data pipeline that includes feature extraction, and the application of a classification algorithm trained to predict quality outcomes. This not only optimizes manufacturing parameters but also provides invaluable insights into the production process, making it possible to anticipate and rectify potential issues before they impact product quality.
Using this data can lead to less scrap, but also to an optimized tool lifetime – which has not only economic, but also ecological advantages.
However, this innovative approach is not without its challenges. The stability of the sensor adaptation and the scalability of the model to accommodate changes in tools, environment and materials are critical factors that must be managed carefully. Yet, the potential rewards far outweigh these risks, offering a path to more efficient, cost-effective and sustainable manufacturing processes.
Looking ahead, the journey doesn’t stop here. The successful implementation of this solution opens the door to further optimization and expansion. Future steps include adapting the control system to new parts and processes and continuously refining the system based on feedback and ongoing analysis.
In Conclusion
The Dentsply Sirona business case within the DAT4.ZERO project represents a leap forward in dental equipment manufacturing. By leveraging the power of process data, Dentsply Sirona is not just improving the quality of its products; it’s setting a new standard for innovation, efficiency, and sustainability in the industry. The next steps promise to further solidify this leadership position, ensuring that dental professionals and their patients continue to benefit from the highest quality equipment for years to come.